
Problem: The customer was upgrading the automation machinery for the manufacturer of gas flow meters. Two components of the meter were different sized pointers assembled on the face of the gauges.
There were three challenges with this feeder system. First, these pointers were very small and light weight. There had to be assurances the new system would eliminate any tangling or misfed parts. Second, the feeder system needed to position the parts with pointers leading to two independent robotic pick up heads. The two heads held two pointers each and one head cycled twice as fast as the other. Third, the customer wanted to consolidate space.
Solution: The two pointers had a geometry that presented a challenge, especially the part with a long-tail pointer. To keep them from lodging in the track with the other parts, they had to be oriented with their tails trailing to move down the track. At the end of the track, each pointer was isolated and completely flipped to orient it for robotic pick up. Fortville engineers designed the system to precisely place each pointer in the indexer nest at the end of the track.
Fortville Feeders designed a two bowl feeder system that fed parts points trailing to two star wheel indexers which rotated them to points leading. Each of the disks held 12 parts, which rotated 30 degrees at a time. One indexer fed 10 ppm and the other fed at a rate of 20 ppm. They used a smart indexer that is programmable to stop at any angle. Older, cam-driven indexers require new cams if the pickup position needs to be changed. The technology employed in these systems gave the end user the flexibility to re-orient parts without building a new feeder system.
Fortville built the system with six vision sensors. Two checked for the presence of parts as they were loaded into the rotary indexer nests. Four sensors checked for the correct orientation of the parts before they signaled the robots to pick up. A Venturi vacuum system picked up any mishandled or out-of-compliance parts to an isolated part return bin.
To accommodate the customer’s space constraints, the two parts feeder systems were mounted side-by-side on a single table. Both of them could be operated independently of the other. The customer was presented a dual feeder bowl system that met their specifications and gave them flexibility to make future changes.
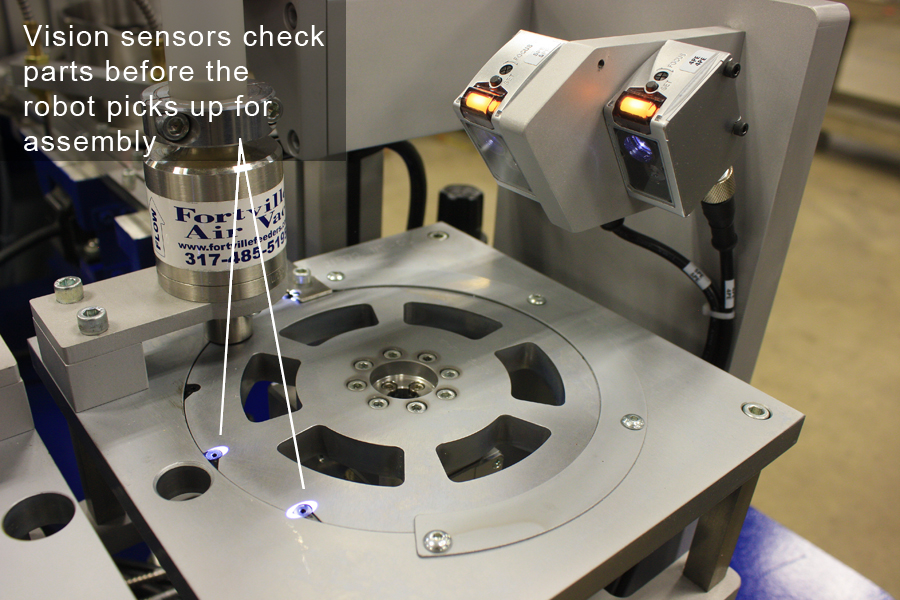
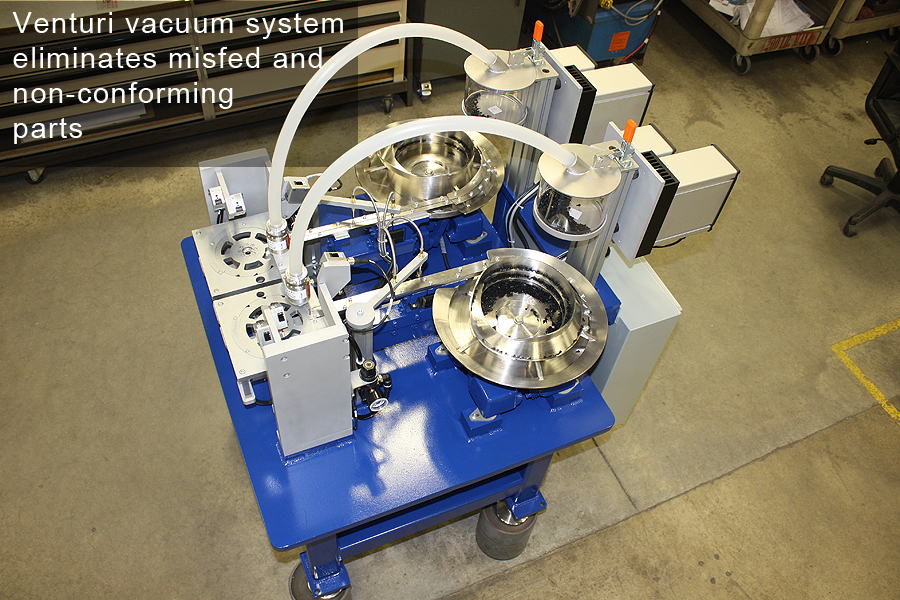
Recent Comments