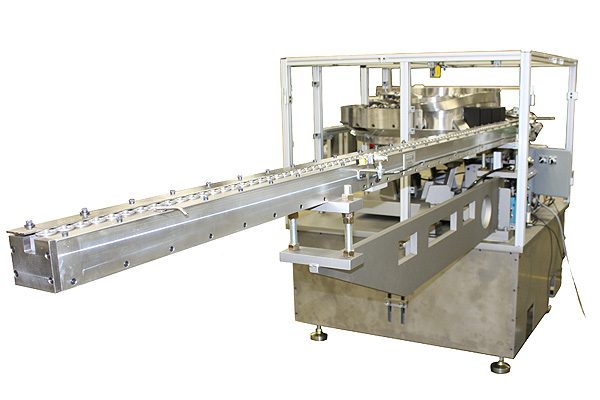
Problem: The customer produces refrigerant recharging cans. They had three different types of auto discharge valves that are assembled as caps on to their cans. They also had different can sizes. They needed a feeder system that could be set up for any of the three topper valves and any of the can sizes through a PLC.
Soution: Fortville designed a vibratory feeder bowl that fed an air driven track. The system was built with three air banks, one for each of the three topper valves. Changeover from one part to the other was controlled by the PLC and no other human interaction was needed. The system also adjusted for the size of each can by lifting or lowering a motorized table. The customer needed the track to cantilever 95 inches past the table to meet their manufacturing floor requirements. Fortville designed the track with booster air jets and optical sensors to make sure each part was moving inline down the track.
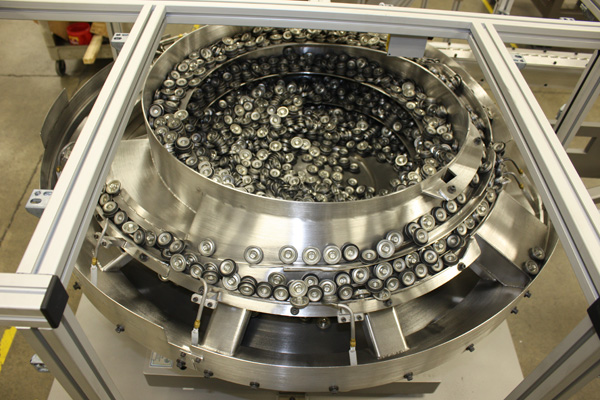
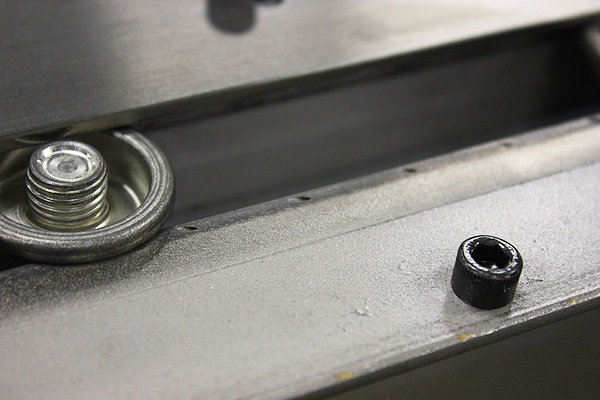
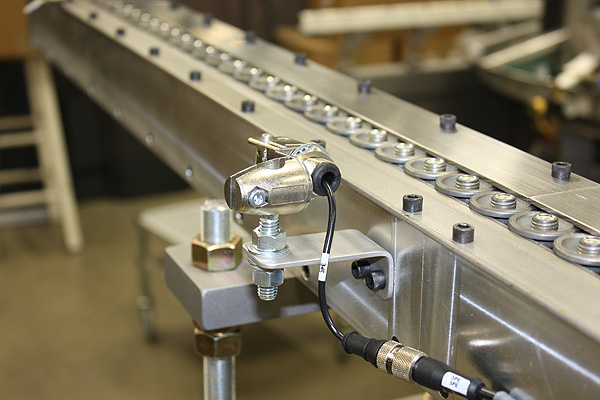
Recent Comments