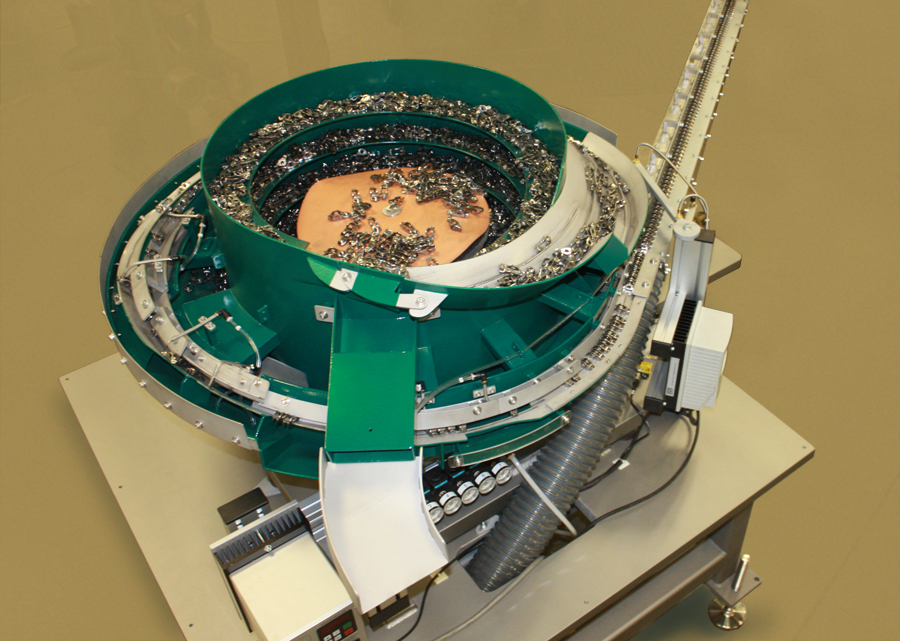
Problem: The customer was building an integrated system for the assembly of auto parts. The automated system required a heavy steel rocker arm part to be presented to a robotic arm and assembled with a bolt and pin. The customer needed a feeder system that could meet some stringent requirements. First, the parts needed to be oriented and moved from a feeder bowl to a robot pick up nest at a high speed without excessive friction on the track. Friction along steel tracks has been known to magnetize parts. This would cause major problems when the three parts were assembled. Secondly, vibratory movement was not an option. The rocker arms were heavy and vibratory tracks would be damaged and have to be replaced in short order. The customer wanted a system that was not constantly down for repairs. Thirdly, compressed air, which is commonly used to move heavy parts, was not an option in this situation.
Solution: Fortville Feeder’s engineers met with the customer and came up with a solution that met their specifications. First, the parts were moved with a forced air blower instead of compressed air. This allowed the parts to glide along the track on air, virtually eliminating any contact with the lower part of the track. Fortville built the track with stainless steel that had a plenum air supply under the track. The track was designed with directional louvers to lift and move the parts. The plenum distributed the air evenly through all the louvers. They were held in place by a top confinement guide that ran the length of the track. The track was manufactured with an austenitic stainless steel, which is a non-magnetic steel that resists corrosion and wear. To protect the top confinement guide from damage, Fortville used a hardened coating on the stainless steel where the parts made contact with the upper section of the track.
Fortville was able to meet the strict specifications of the customer and provide an engineered solution. The feeder system moved parts up to 185 ppm without damaging either the parts or the tracking system.


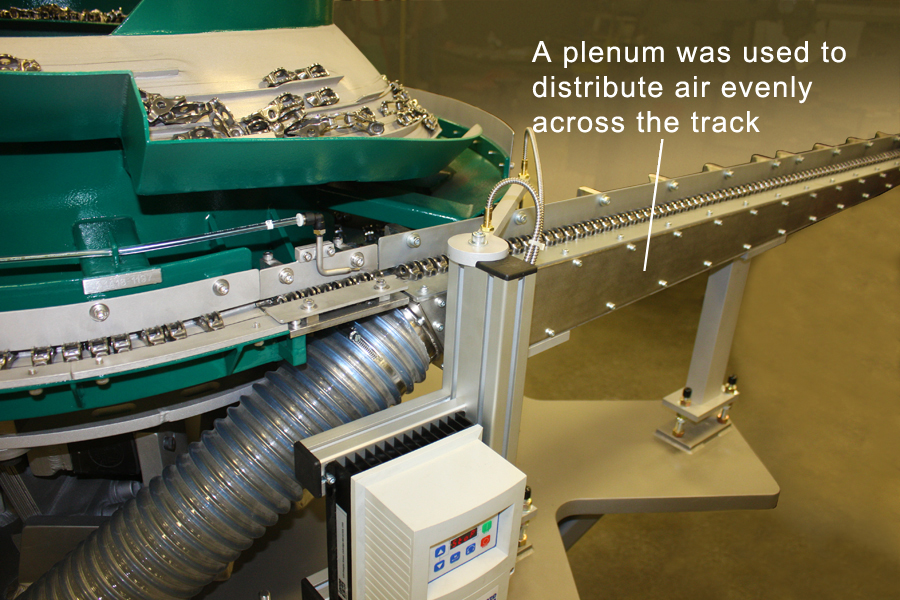

Recent Comments