Solution: Fortville Feeders designs feeder systems with duplication in mind. Each system is designed with a set of blueprints that are archived and can be replicated or reworked to redesign a parts feeding system.
Designing a feeding system starts with the size and geometry of the part compared to the needs of the customer. In this case, Fortville had to size the centrifugal bowl to accommodate the large parts. It also had to ensure the hopper had the capacity for the parts and the cleated elevator was sized properly to keep up with demand. An oversized hopper was used that could be filled to capacity and supply parts for 20 minutes at full speed. The elevator was also encased with Lexan guides to keep the long parts from tumbling to the floor.
Fortville also designed the feeder system so that it could be sped up to feed parts up to 120 parts per minute. This enabled the customer to increase production speeds without revamping the feeder.
In the end, the customer had a duplicate centrifugal feeder that moved parts quietly and quickly to their assembly station. It was engineered to provide adjustable speeds. The system was built large enough to fit the operational requirements desired by the customer.
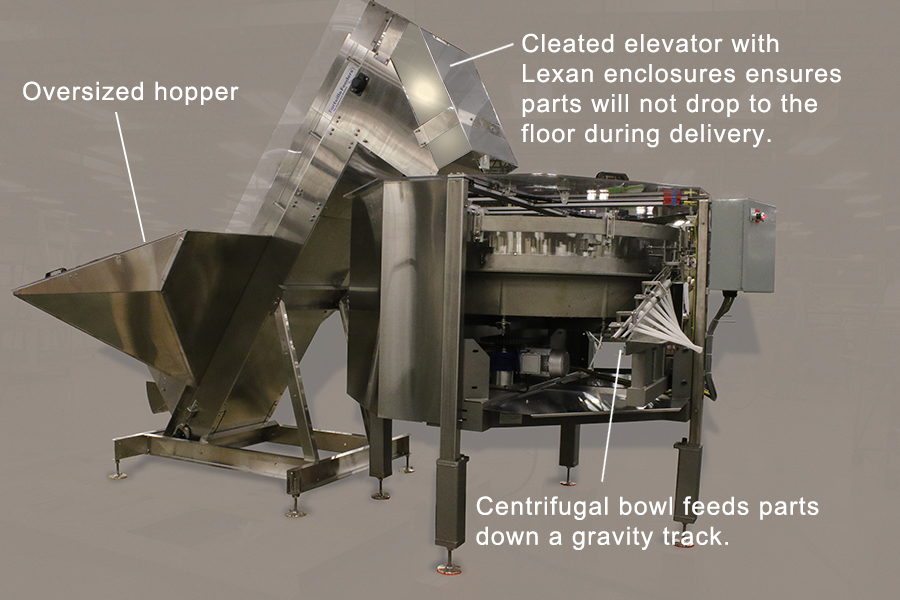
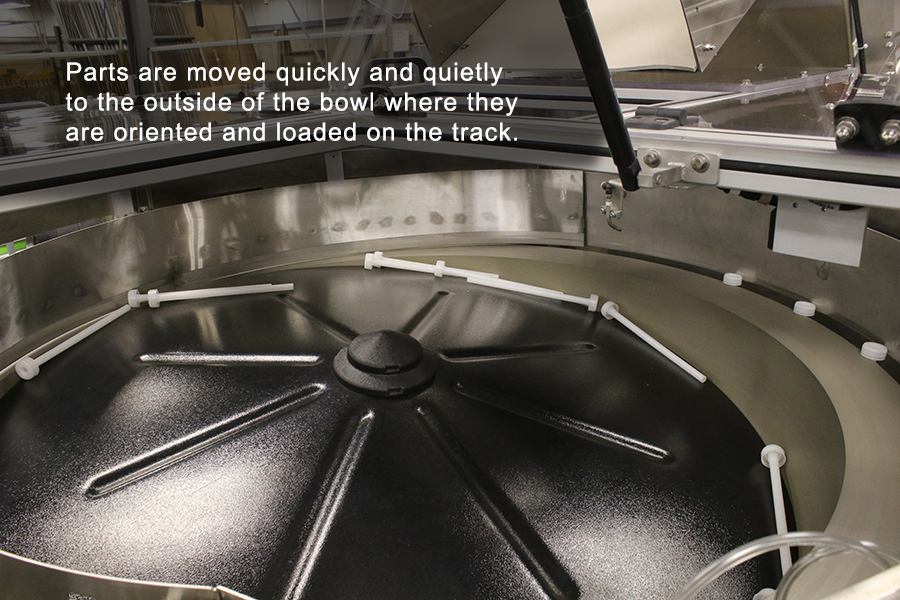
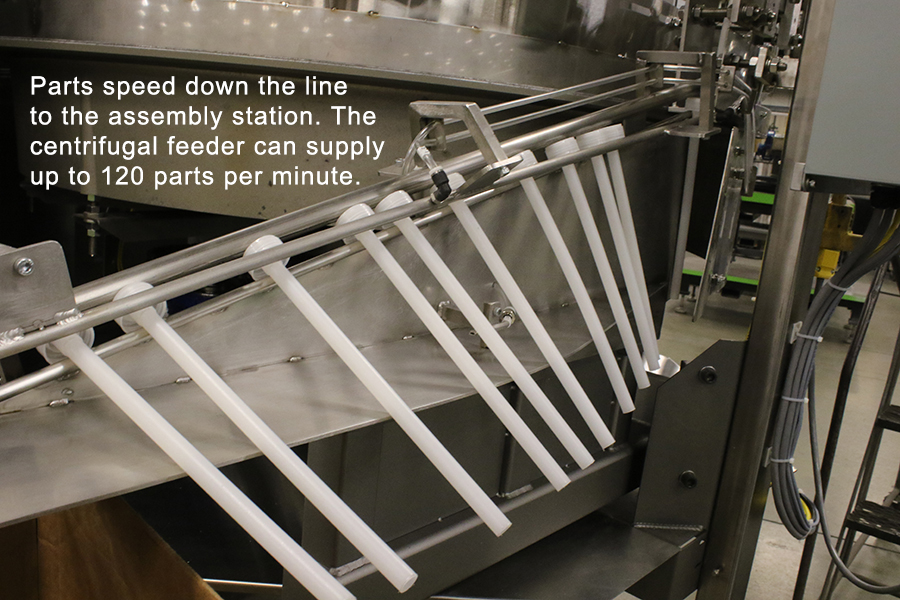
Recent Comments