Problem: The manufacturer of plastic containers was in need of an automated feeder system for their closure components. They needed a high-speed system that would handle the molded plastic parts without clogging the machine while supplying their assembly lines at 200 parts per minute. The system also had to fit into a confined space and align with the assembly line, as well as operate with its own air supply system.
Solution: A critical part of Fortville Feeders’ design process includes a meeting with the customer’s engineers to discuss part delivery and handoff. This communication is critical to the engineered solution that Fortville provides their customers. In this case, there were three critical components to achieve a successful feeding solution: moving the molded parts quickly without clogging the machine, fitting the limited space for the assembly area, and building a self-contained air system to move the parts without using compressed air.
Fortville designed a feeder supply system that kept the parts moving and took into consideration that these are plastic parts with parting lines and flash that cannot be completely eliminated. Before each part was placed on the delivery track, a vision system checked that the parts were within tolerance for short shots or damage. The lightweight parts had to be held in place while moving down the track at high speeds. The air track is was more than capable of performing this task, but, for peace of mind, the customer requested an o-ring conveyor to be added as a redundant system to ensure flashing would not slow down the line of parts. The o-ring conveyor was synced with the speed of the air track and moved any part that posed a clogging threat due to excess flash.
The space restrictions required that the parts be turned 90 degrees to align with the assembly line. A turn like this also could pose a clogging threat. In order to make this work, the air had to be regulated within the track. Fortville’s expertise in understanding part geometry and the volume of air needed to move each part down the line was key. Fortville has in-house EDM drilling capabilities that allowed them to not only control the spacing of air holes in the track, but also the angle and shape of each hole. This was coupled with an air control manifold system that regulated the air in different areas of the track. This allowed the operator the ability to adjust the air required to the move the parts in different areas along the track.
Since the customer did not want to use a compressed air system that was piped to the machine, Fortville built the machine using a forced-air blower with a plenum for air track controls. One of the added benefits of using a blower is the reduction of noise that is common to compressed air.
Fortville’s design and expert tooling proved to be a success in meeting the customer’s design requirements. They ordered three more duplicate machines.
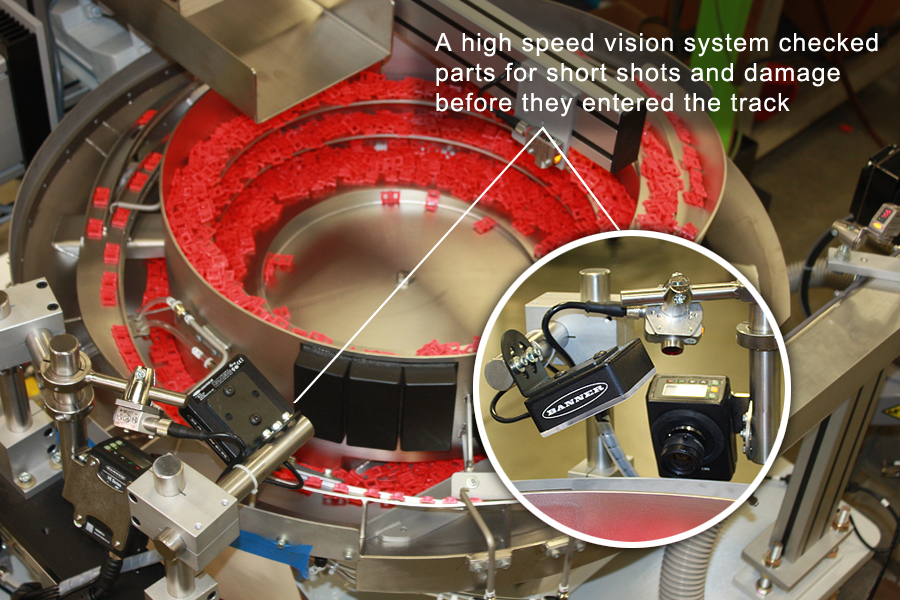
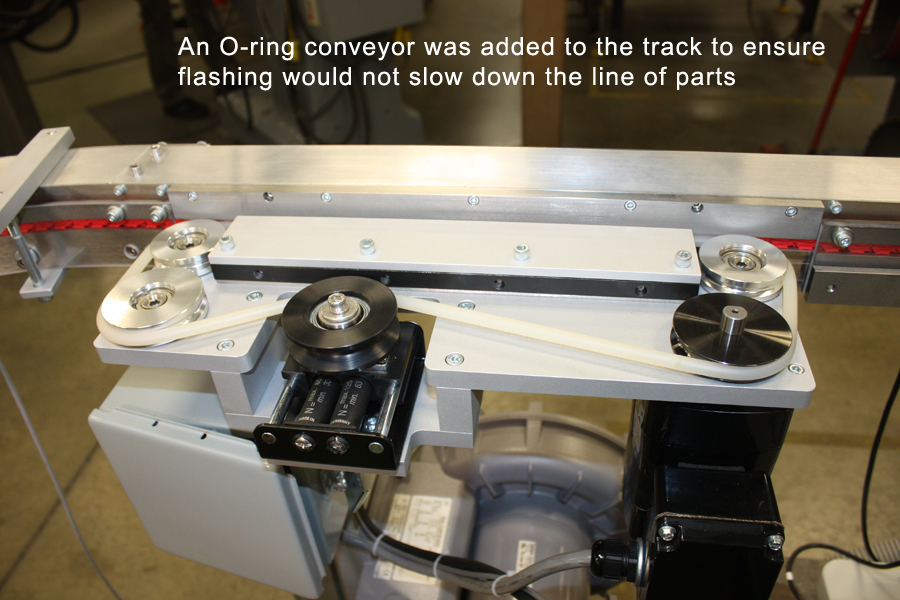
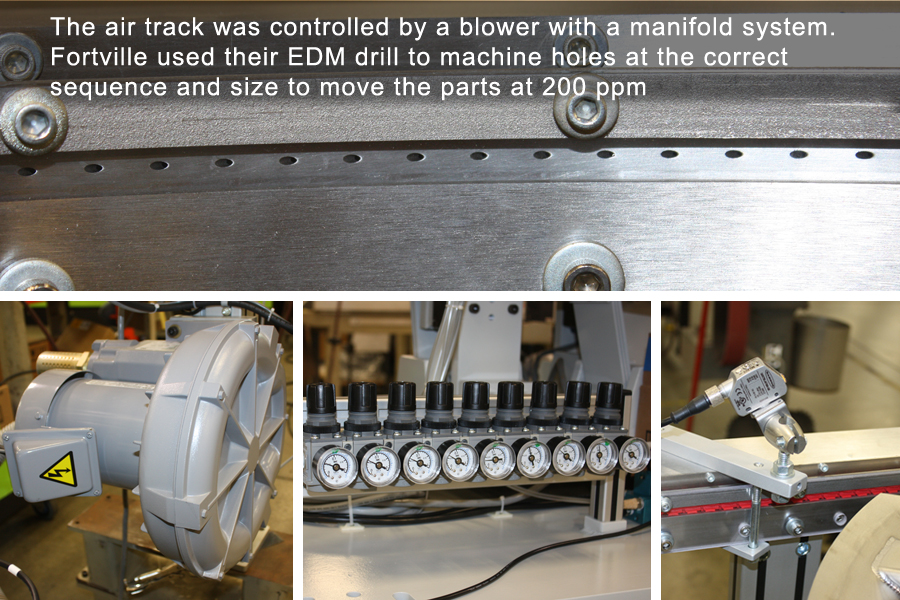
Recent Comments