Problem: A medical packaging integrator was in need of bulk feeder systems for their vial assembly operations. They had a contract with a worldwide leader in biotechnical and pharmaceutical testing to integrate eight new parts feeder systems into their existing packaging equipment. With the demand for body fluid sampling growing in the shadow of a worldwide pandemic, there was suddenly a high need for more blood sampling vials. The integrator needed to accelerate their manufacturing process. However, the integrator could not afford to have any problems with feed rates, misoriented parts or sanitation concerns with the feeder. The customer needed to rush these eight new systems into production.
Solution: Fortville Feeders had the expertise and capacity to offer a solution without cutting corners. That started with the materials used to build the systems. Most medical equipment come with a set of very strict sanitary and human handling rules. In this case, it was necessary that no human hands touch the vials through the entire feeding and packaging process. Fortville designed eight feeding systems that were completely contained within a medical-grade stainless steel enclosure. The eight feeder systems were designed to use 316 stainless steel instead of the more common 304 stainless steel that many other feeder builders use. Fortville stocks 316 stainless as a standard in all of their medical grade feeders. The difference is that 316 stainless steel uses a molybdenum alloy for extra corrosion resistance against the chlorides used to clean and disinfect stainless steel components. Since Fortville stocks the higher grade of stainless steel, the lead times on the manufacturing of these systems was significantly shorter. Fortville also has the testing capabilities that many medical/clinical end users require to prove conformity to the 316 standard.
Lexan doors and windows in the top of each unit allowed the operator to monitor the progress of the parts without contaminating the sterilized area. These doors were framed in with extruded aluminum casing that was fit with a plastic seal that kept airborne contaminants from settling in the grooves of the frame. When the bowls were empty and each system was sterilized, the Lexan doors were lifted for quick access to the bowl and track.
Beyond materials, fit and finish, each system had to accurately move a variety of vials at a high rate of speed. Fortville’s engineers had to take into consideration the many number of products that would be fed by the systems and design them for flexibility. For instance, one feeder system handled six different vials, all with slightly different geometry. All the vials were fed with caps intact. Some caps were cylindric, some were designed with flat gripper sides. The main body of the vials also differed in size and shape. Fortville’s parts feeding expertise allowed them to design and build solutions that made each feeder system work precisely for any number of vial sizes and geometries.
The customer was able to integrate the feeder systems into their assembly automation and put the eight lines into service without any problems. All medical/clinical specifications were met and each feeder system was cohesive with the existing automation.


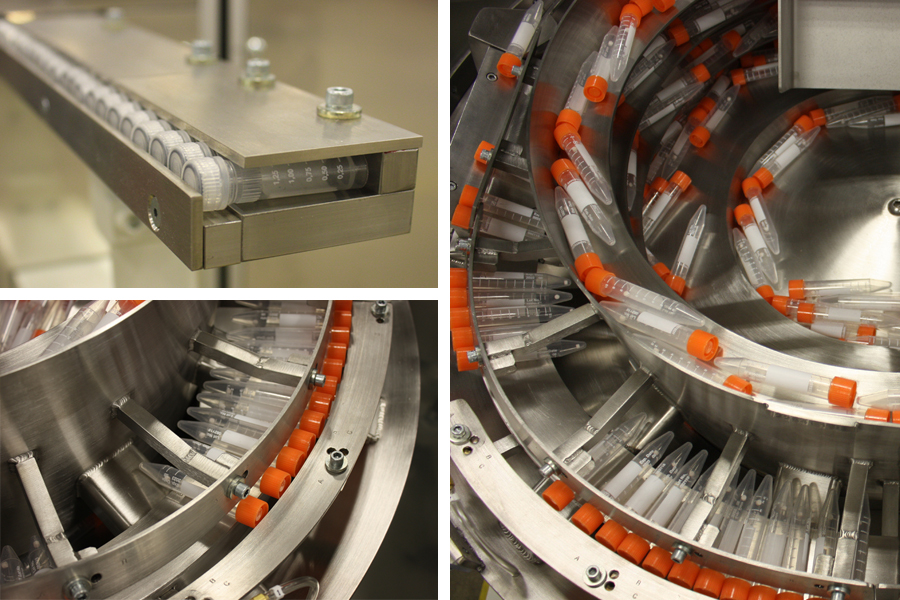
Recent Comments