Problem: The manufacturer of hand sanitizer bottles desired a single feeder system for multiple foaming pump nozzles for their automated bottling assembly station. They had five different pump nozzles that were of different sizes and geometries. Some of these pump nozzles had a cap and others did not. The delivery system also had to adjust to multiple heights at the capping station based upon the height of the bottle being filled and assembled.
Solution: Fortville Feeders has decades of experience designing and building parts feeders for odd-shaped parts in multiple-use systems. That expertise comes with an understanding of how to design multi-part systems that can be changed over easily.
There were three key design elements to a quick changeover. First, the feeding system was designed to make all of the changeover adjustments to the linear track. The tooling in the feeder bowl had one blade to swap out depending on which family of pump nozzle that was being fed. Second, the delivery track was built with an adjustable angle to accommodate the different bottle heights at the end of the track. The machine operator could simply crank the discharge of the track up or down to meet the desired height in a matter of seconds. Third, the tooling on the delivery track was designed to hold a centerline on all the nozzle lids, regardless of size or geometry. The track confinements were adjusted with positive stops for the height and width of each family of pump nozzle. Leftover parts in the hopper were quickly changed out with the addition of a quick-dump door. The entire changeover only took a couple minutes, compared to nearly an hour for the rest of the line.
The other unique aspect of the delivery track was the use of EDM holes to direct compressed air to assist the pump nozzles down the slight angle of the gravity track. Fortville designed air tracks are quiet, sturdy and use very little air. This track cost pennies per day to operate. Having a smoothly running track allowed the system to deliver parts at a rate of 100 per minute.
In the end, Fortville produced a parts feeding system that could deliver multiple pump nozzles, which provided the end user with tremendous flexibility in their manufacturing process.


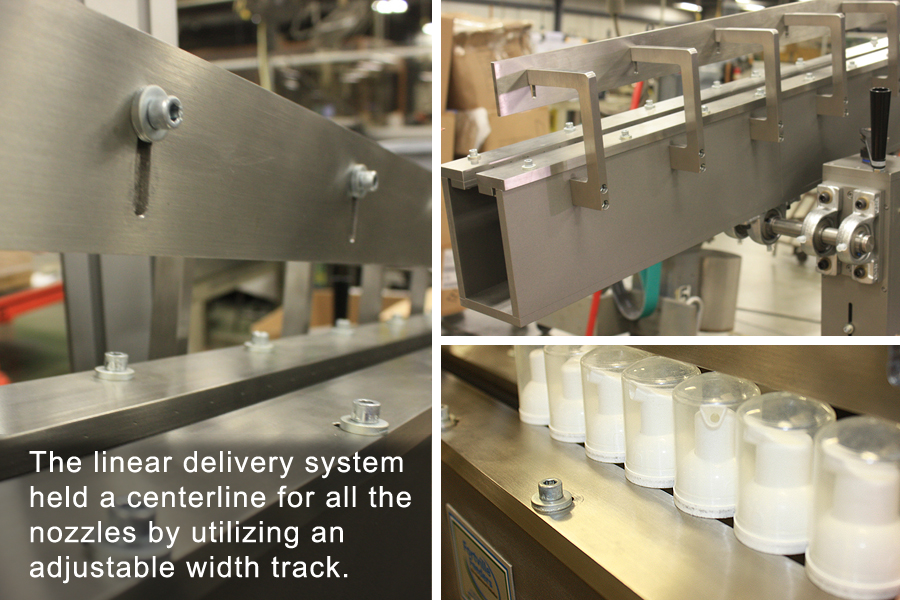
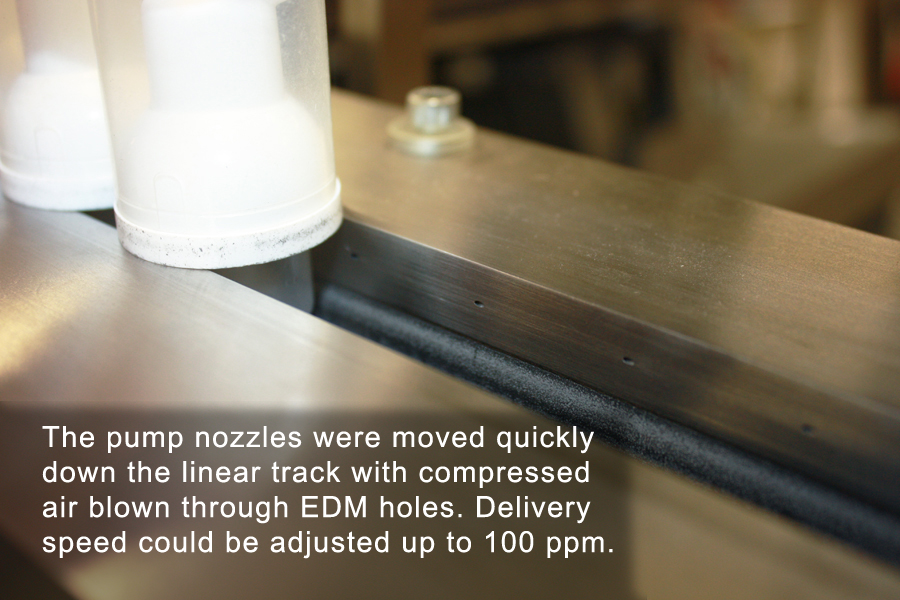

Recent Comments