Problem:
A manufacturer of syringe filling machines needed a complex parts feeding system. They were designing a system for operations in a C1D1 manufacturing environment where highly flammable and explosive material was being used. That required no electrical wiring outside of a sealed explosion container. All of it had to be air-generated in terms of moving bulk parts, including any vibratory movement. Since they were dealing with syringes, the system also had to be sealed in such a way that no particulate matter in the air could come into contact with the parts and cause contamination.
Solution:
Fortville Feeders designed and built a vibratory feeder system that used an air-driven ball vibration system to move the bulk parts in the bowl to the track. Once they were singulated, they were oriented and driven down the track with pressurized air. The entire machine was run by an intricate air valve system.
All of the electrical components, including the drive for the bulk hopper and elevator, were housed in a sealed explosion chamber so there was no chance of a spark in the open environment.
Fortville also built an enclosure around the elevator discharge, feeder bowl and track to seal out any airborne contaminants. FDA requirements were followed. Precautions were also made to keep random parts from bouncing out of the bowl and knocking fragments of the door materials loose. The foam of the enclosure doors was sealed with metal sheeting to keep it from breaking free and contaminating the parts. Fortville also built the system using 316 stainless steel to meet FDA regulations.
At the end of the line, the parts were isolated and handed off to be metered one at a time. Fortville designed a cross shuttle that worked with the customer’s metering system.
Fortville delivered a feeder system that not only provided spark-free movement of parts to meet C1D1 classification guidelines but also built a system that met the FDA standards needed for handling sterile parts.
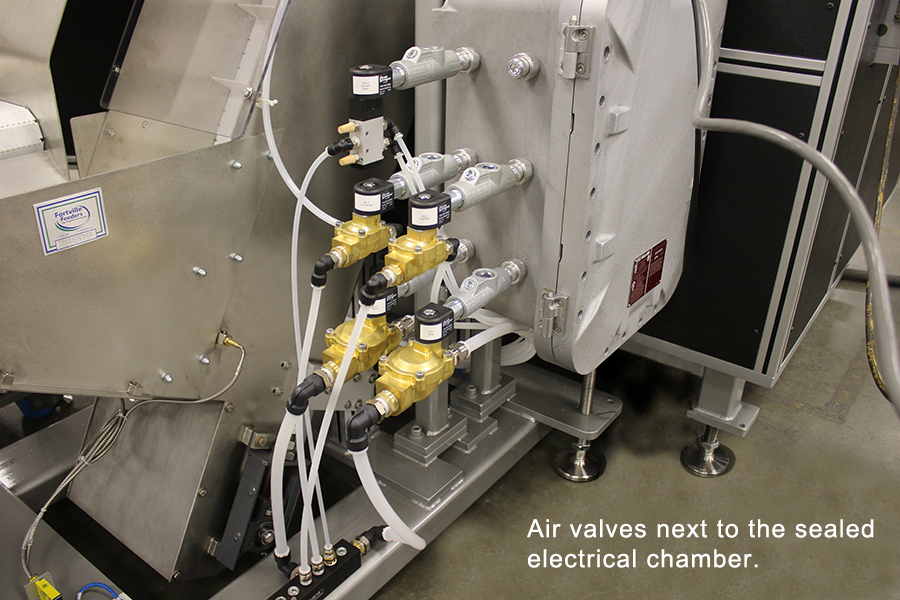
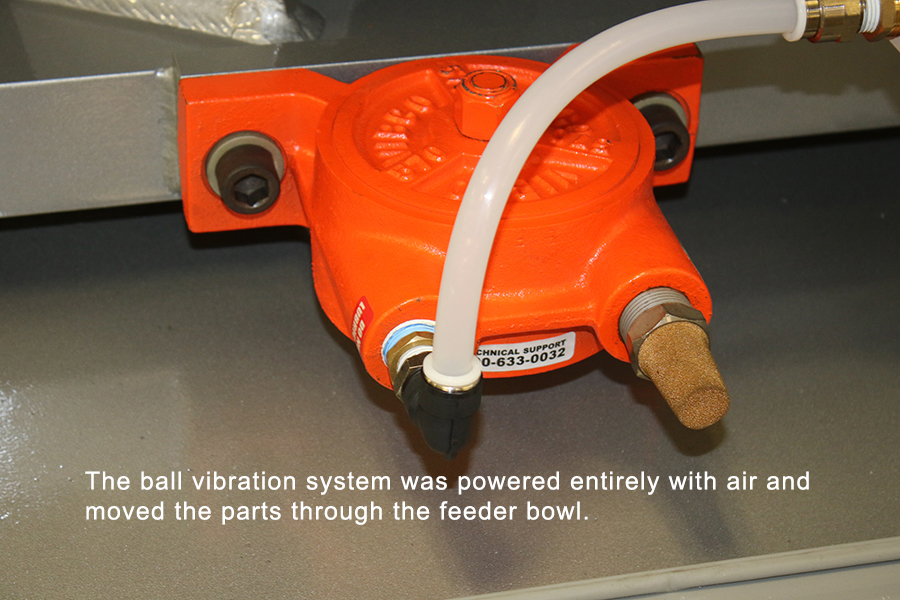
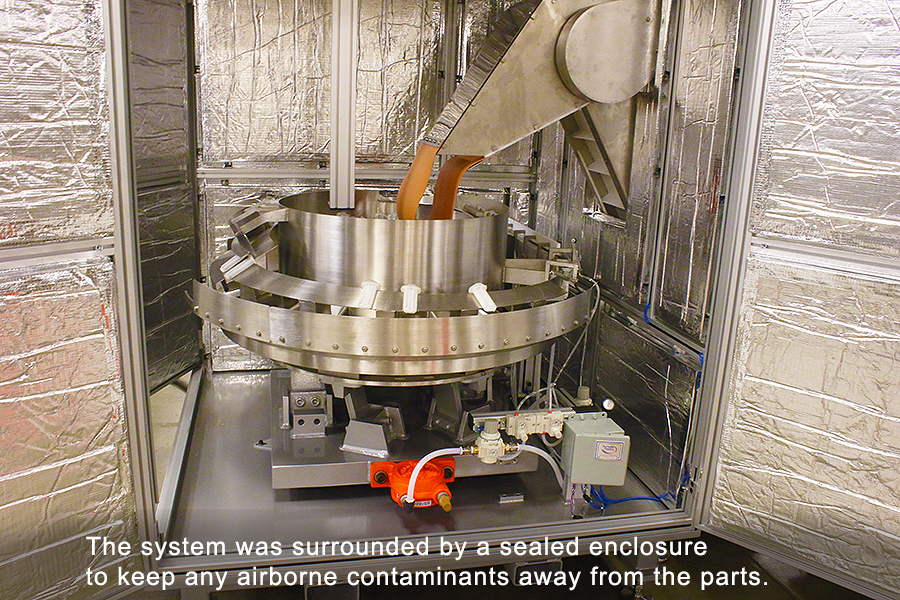
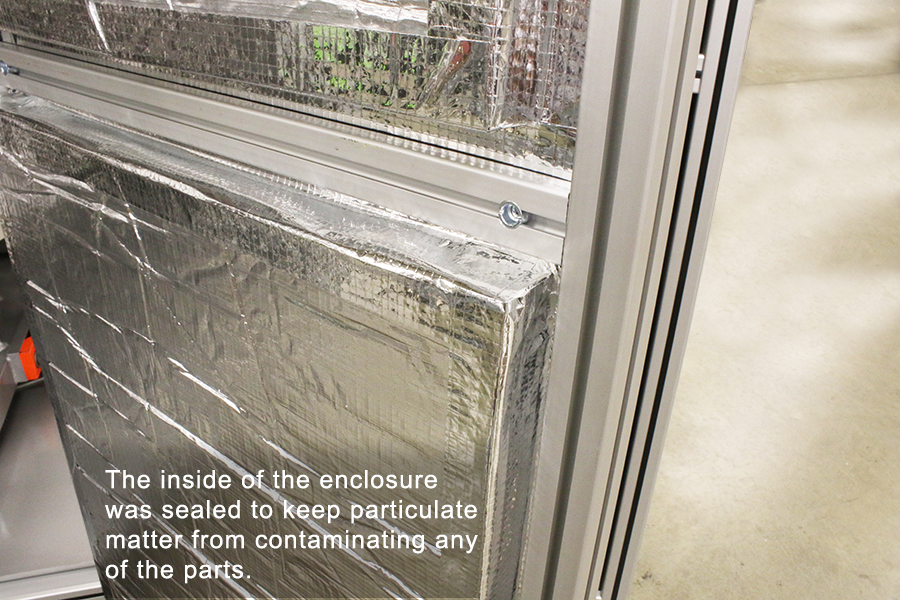



Recent Comments