Problem: A medical device manufacturer needed to replace an inefficient feeder system for two caps. The system they had attempted to feed two parts from the same vibratory bowl. The two caps had very different geometries. It caused constant jams in their old feeder. They sought out Fortville Feeders for a new solution to their parts feeding problem.
Solution: The customer had limited space to place the feeder system into their assembly line. However, rather than placing both parts in the same bowl, Fortville came up with a two-bowl system that used a common inline track for both parts. This saved both space and reduced the cost of the machine.
The machine was built using 316 stainless steel for the bowl, tooling and track to meet the medical requirements of the project. The customer had very specific needs when it came to the end of the line. The system integrated with a pick-and-place robot to pull parts from either line upon demand. Up to five parts were pulled per cycle. Fortville used a dual dead nest with parts sensors to backfill the lines. The parts sensors were set back from the end of the line to accommodate a full cycle of parts.
In the end, Fortville’s expertise in building parts handling system gave the customer a reliable feeder system that worked well with their assembly system. The two bowls and one track fit the space they had on the manufacturing floor and kept the parts moving free of jams.
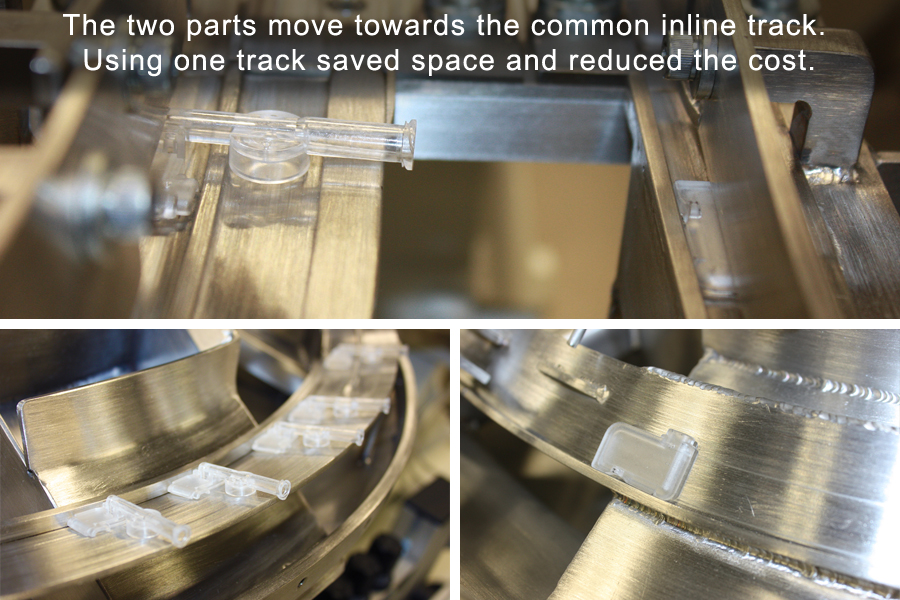

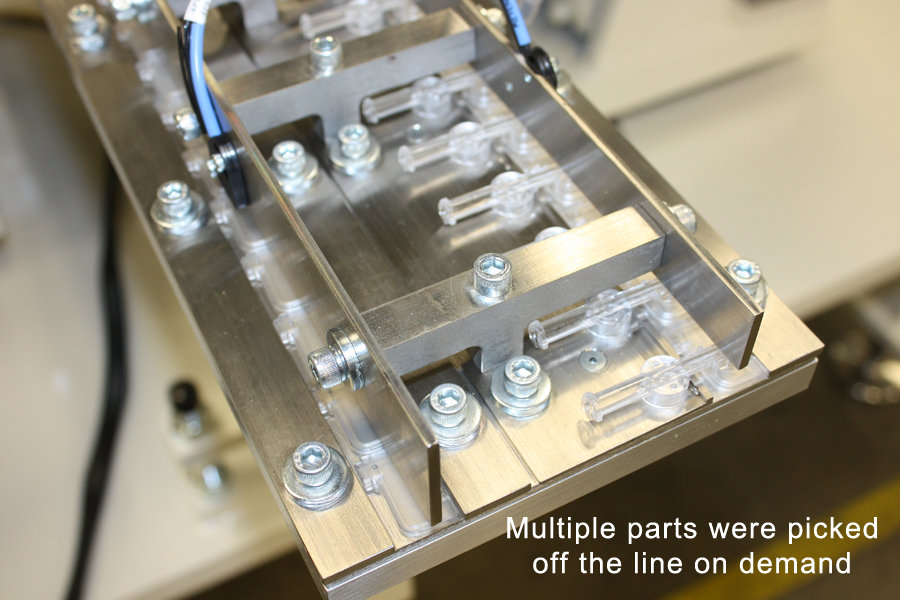
Recent Comments